Neue Längsteilanlage Sennwald
Teil 2 der Baureportage: Bodenplatte und Maschinenmontage
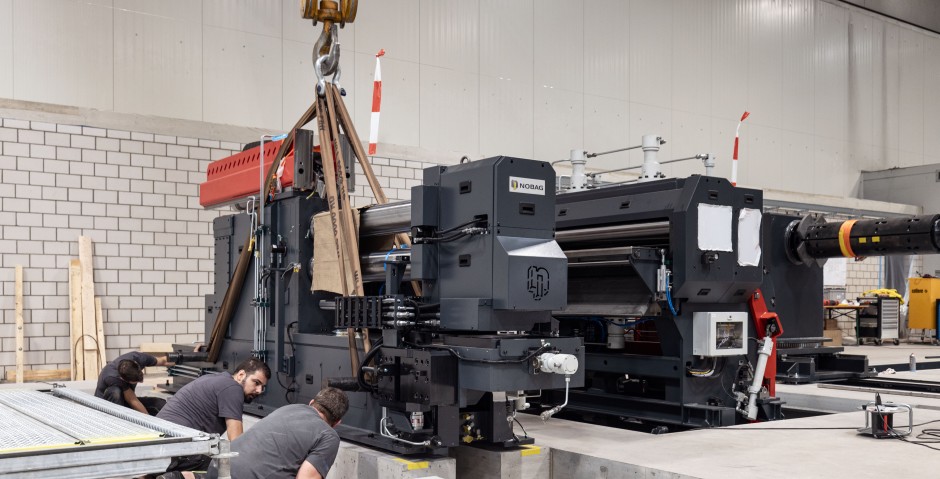
Beschäftigten uns im Winter noch die Schlingengrube und Taucher, widmen wir uns nun bereits der Montage der neuen Längsteilanlage. Bevor es jedoch so weit kommen konnte, stellte uns der Hallenboden vor einige Herausforderungen.
60 Mikropfähle im setzungsempfindlichen Untergrund sorgen dafür, dass der Boden die tonnenschwere Anlage hält.
Die ersten Schwierigkeiten offenbarte der nicht sichtbare Teil des Hallenbodens. Ein geologisches Gutachten attestierte einen setzungsempfindlichen Untergrund. Damit der Boden die tonnenschwere Anlage hält, wurden 60 Mikropfähle bis zu 12 m in den Boden, zu festem Untergrund, gerammt. Anschliessend wurden die Pfähle ausbetoniert und mit der 630 m2 grossen neuen Bodenplatte verbunden, auf der u.a. die Längsteilanlage steht.
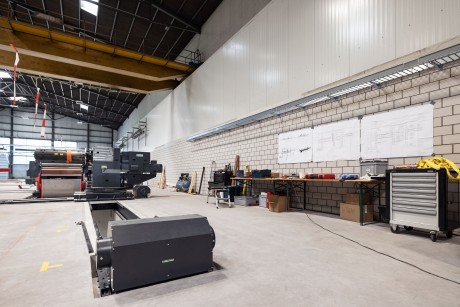
Bodenplatte: nur 0.2 mm Ebenheitstoleranz auf 30 m
Da die neue Längsteilanlage kaum Toleranzen in ihrer Positionierung und ihrer Ausrichtung zulässt, darf sich die bis zu 1 m dicke Bodenplatte unter der Anlage nicht durch deren dynamische Kräfte oder deren Gewicht verändern. 40 t Bewehrungsstahl in der Bodenplatte waren nötig, um eine Ebenheitstoleranz von lediglich 0.2 mm auf 30 m zu erreichen.
Leitungen im Boden verlegt
Auch die bis knapp 2 m tiefen Schächte für die im Boden zu versenkenden Hubaggregate waren millimetergenau auszuführen. Zudem wurden alle Kabelkanäle in die Bodenplatte eingelassen. Die Leitungen in den Boden zu verlegen, ist wartungsfreundlicher und erhöht die Arbeitssicherheit.
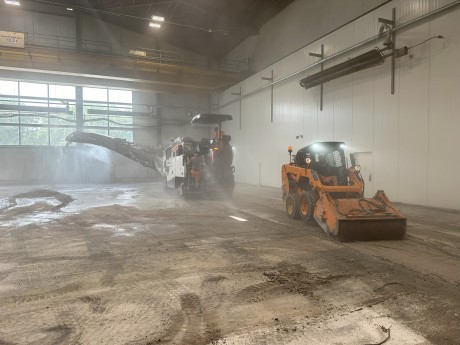
Anschluss an alten Hallenboden schwierig
Nachdem die plane Bodenplatte erstellt war, wurde der restliche Hallenboden ausgeglättet. Durch Nutzung über viele Jahre hinweg und die damit verbundenen Belastungen haben sich unterschiedliche Setzungen ausgebildet. Für einen sauberen Anschluss des neuen Bodens an die bestehende Bodenplatte mussten wir den alten Belag auf 2 m Breite ausfräsen und mittels Monobeton einen Übergang schaffen. Damit ist die logistische Unabhängigkeit zwischen Maschine und Lager gewährleistet.
Über 100 m langer Fluchttunnel
Eine Auflage beim Baugesuch war ein Fluchttunnel entlang der Hallenwand. Er ist aus Kalksandstein gemauert und über 100 m lang. Im Falle eines Brands in der Halle gewährleistet er den sicheren Weg ins Freie.
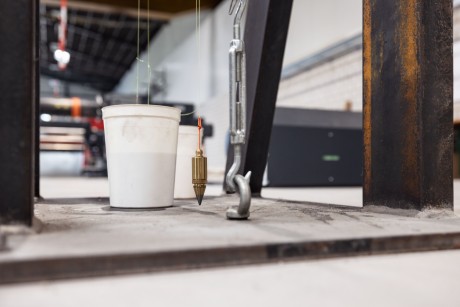
Belagsfräse am Limit
Die neue Bodenplatte für die Maschine wurde im hinteren Teil der Halle erstellt. Im vorderen Teil, bei der Anlieferung des Rohmaterials, war noch der alte Belag zu finden. Statt ihn rückzubauen und zu ersetzen, entschieden wir, ihn abzufräsen. Diese Arbeit sollte eine Belagsfräse erledigen, wie sie beim Autobahnbau eingesetzt wird. Dass der 1'200 m2 umfassende Boden in diesem Teil der Halle extrem stark armiert war, brachte die gewaltige Maschine an ihr Limit. Fast wären die Arbeiten abgebrochen worden. Schliesslich jedoch schaffte die Maschine ihren Auftrag. Nach dem Abfräsen wurde eine etwa 3 cm dicke Monobetonschicht eingebracht. Am Ende wies die Halle einen einheitlichen Bodenbelag auf.
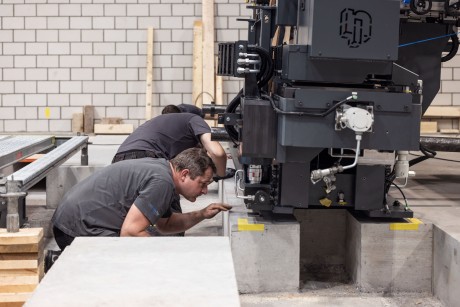
Montage mit Schnurgerüst und Senkblei Während sich in der einen Hallenhälfte die Belagsfräse abmühte, schritt in der anderen Hallenhälfte die Montage der Längsteilanlage voran. Um diese Arbeiten von dem beim Fräsen anfallenden Staub zu schützen, spannten wir eine monströse Plastikwand von der Decke der Halle bis zum Boden. Ein Gerüst aus Stahlschnur über der Maschine und Senkblei garantiert den exakten Aufbau der Anlage. Dies ist die zuverlässigste Methode, um die Maschine auf ein Zehntel mm genau auszurichten.
Ausblick stimmt zuversichtlich
Die bauseitigen Arbeiten sind abgeschlossen und die Anlagekomponenten stehen. Derzeit werden rund 200 km Elektrokabel verlegt und angeschlossen. Anschliessend gilt es die Steuerung zu programmieren. Wir sind zuversichtlich, die Anlage Ende September in Betrieb nehmen zu können.